旋转隔板对中压缸效率影响(一)
双侧进油旋转隔板油动机常见问题分析
双侧进油旋转隔板油动机常见问题分析
大唐保定热电厂
检修部汽机专业 吴仲涛
摘要
通过我厂10、11号机近年来旋转隔板油动机故障造成的EH油泵油压降低造成联泵、油动机无法开启等相关问题,对旋转隔板油动机的构造及系统进行分析,为同类机组以及类似故障的处理提供一定的参考指导意义。
关键词
快速卸荷阀 缩孔 EH系统油压 伺服阀零位偏移
前言
我厂10、11号汽轮机为哈尔滨汽轮机有限公司制造的超高压、一次中间再热、单轴、双缸双排汽、双抽调整抽汽供热凝汽式两用机组。机组型号N200/CC144-12.75/535/535/0.981/0.245。工业抽汽流量由装在中压缸的第12级旋转隔板来控制,旋转隔板油动机(低压抽汽调节阀执行机构)属控制型执行机构,采用双侧进油式油动机,油缸侧装有伺服阀、卸载阀、快关卸载阀、快关电磁阀各一件。可以将低压抽汽调节汽阀控制在任一位置上,成比例地调节抽汽量以适应汽轮机抽汽运行的需要,同时也可实现快关要求。油动机在正常运行时为双侧进油,EH油分别由压力油管和有压回油管路进出。当一侧压力大时将活塞压向另一侧,活塞杆相应伸出或缩回。油动机为倒装形式,当活塞杆全部伸出油动机全关时旋转隔板为关闭状态,反之为开启状态。
案例介绍
1、2012年09月10号机A级检修后期在油动机返厂检修运回组装后做系统静止实验时发现,油动机不能开启。因检修中旋转隔板重新加工,为防止做实验挂闸后因系统压力升高旋转隔板自行开启时有其他问题,所以在挂闸前将此油动机进油门关闭,欲在实验时单独打开进行测试。当打开进油门后因活塞上部油压大于下部油压将活塞杆全部压出,使旋转隔板处于关闭状态。用手动操作控制仪器(简称手操器,下同)接入伺服阀接口进行开关测试时发现油动机无法打开。在手操器加大电流信号后进行开关测试,能明显感到油管路中因油压变化产生的震动,但油动机没有相应开关变化。在确认回装油动机前旋转隔板开关自如无卡涩后对油动机进行重新分析。更换新的伺服阀后、更换电磁阀、检查伺服阀、电磁阀的电源和信号线路没有发现问题。再次试验时发现,如果关小进油门至接近关闭位置并加大手操器电
流,油动机可以缓慢开启,但无法保证油动机正常运行。
参照系统图进行问题分析,初步判断油动机内的电磁阀、卸荷阀、快关卸荷阀都有造成此问题的可能。将现场照片、系统图纸发送EH维护厂家,在确认部件位置后进行现场拆装检查。拆下伺服阀、卸荷阀压块。取出卸荷阀弹簧,阀体,检查阀口、底口均无磨损,裂纹及夹杂异物等问题,并为防止因弹簧老化强度张力不够的问题,在弹簧座内加入2mm厚垫片,回装后没有解决。将垫片撤下,拆下电磁阀,检查电磁阀下的缩孔,拆下快速卸荷阀压块,更换逆止阀备件,检查后均无问题,加装垫片回装后测试问题依旧。至此油动机上所有可拆卸部件全部检查完毕,没有发现问题原因。换上由厂家带来的专为双侧进油油动机准备的MOOG4型伺服阀(在装均为MOOG3型)问题依旧。在再次检查缩孔时发现,缩孔外露面直径约1mm,而另一端只有大约0.7mm孔径,并没有完全打通,将缩孔拆除进行试验,油动机开关速度正常。为不影响快速关闭将缩孔扩大至3mm孔径装回,故障排除。
2、2013年03月10号机结束停备消缺,在开机准备过程中,开启防止因停机冷却造成旋转隔板卡涩而关闭的油动机进油门后,约20分钟左右,运行人员发现EH油压持续降低,最低降至8MPa左右引起低油压联泵保护动作,2台EH油泵同时运行来维持压力,停止任意一台EH油泵均无法维持压力稳定。在现场检查无任何外漏泄油情况及油箱油位保持稳定的情况下,进行系统的检查。就地检查EH工作站2台油泵运行时出口压力表14.5MPa,EH危急遮断块前AST、ASP、OPC压力表均为0,润滑油泵开启,启动油泵未开启,隔膜阀上油压为0,透平安全油系统未挂闸,检查AST、OPC电磁阀得失电状态正常。盘前检查打闸按钮处于按下打闸状态,复位后没有变化。
在开启启动油泵挂闸后,透平安全油建立,隔膜阀关闭后就地AST、ASP、OPC压力表指示正常位14MPa,停止一台EH油泵运行,系统压力不变。再次打闸后EH油压继续下降依旧报警联泵。考虑当天做调速系统静态试验时一切正常,油压降低属于突发现象,在此期间EH系统只打开过旋转隔板油动机进油门,随即到现场检查发现,在热控信号仍为100%强制开启条件下,油动机已关闭(活塞杆全部伸出,盘前反馈显示关闭状态)。重新2台泵运行挂闸后将旋转隔板油动机开启,后关闭进油门进行强制,停止一台泵运行,压力正常,打闸后一台油泵压力正常,挂闸正常。
3、2013年10月11号机A级检修在油动机返厂检修运回组装后做系统静止实验时发现,油动机不能正常开启。首日试验挂闸后阀门开关正常。次日调试即将结束打闸后重新挂闸进行确认时发现旋转隔板油动机无法打开。在确认热控信号、插头接线无损伤后用手操器进行就地试验,仍旧无法开启阀门。在更换伺服阀后故障没
有消除,更换其他正常阀门取下的电磁阀问题依旧。按照12年10号机大修经验决定拆卸快关卸荷阀组块进行检查,解体后发现阀体内部存有一直径约8cm红色橡胶封堵,经维修厂家确认此封堵为外部油口防尘用,不知何故忘记检查取出,造成卸荷阀泄油、油动机开关故障。卸荷阀组块清洗回装后测试一切正常,问题解决。 原因分析
1.1 造成油动机无法关闭的原因为油缸内部上腔室压力大于下部压力,在相同作用面积下压力大的活塞上部油压一直将活塞压向下部,使活塞杆压出油动机。
1.2 造成油缸内上部压力大于下部压力的原因为通过电磁阀到快关卸荷阀和卸荷阀上部的安全油压降低油量减少、致使2个卸荷阀无法完全关闭泄油口。快关卸荷阀的泄油直接流回油缸上部,卸荷阀的泄油无法进入油缸下部而直接流回油箱。
1.3 造成安全油压降低的原因为快关电磁阀下部缩孔孔径过小,进油量进油压力减少。
1.4 缩孔直径过小的原因:
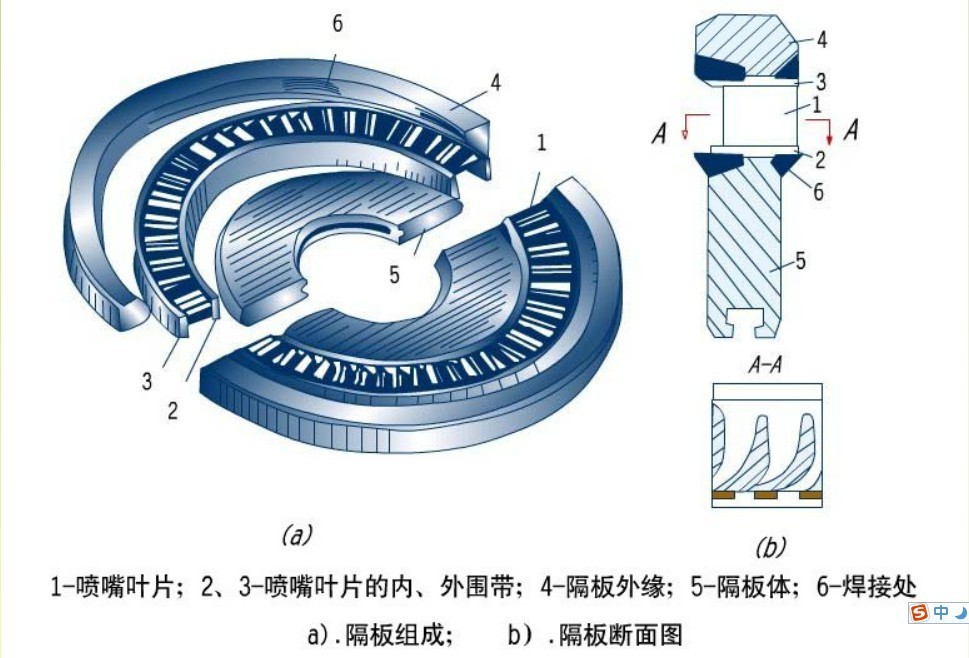
1.4.1 经了解油动机返厂检修时将缩孔拆除,厂家不慎将原缩孔丢失,重新加工的新缩孔。
1.4.2 因油动机为哈尔滨汽轮机有限公司产品,修理厂家并无油动机详细图纸。所以在试验台上进行试验时,因试验油压低于机组正常运行时的油压,将缩孔孔径定为1mm时并无问题发生。
附图1-旋转隔板油动机系统图
有压回油 卸荷阀压块
伺 服 阀
无压回油 压 力 油 快关卸荷阀压块 电 磁 阀
附图2-油动机集成块外观 OPC油管
附图2-油动机集成块外观
OPC油管
快关卸荷阀 缩孔相对位置 逆止阀
旋转隔板对中压缸效率影响(二)
210MW汽轮机旋转隔板故障原因分析及处理
210MW汽轮机旋转隔板故障
原因分析及处理
赵 伟1 黄 智2 王晓峰1 郭广富2 齐贺楼3
王予生2 贾宪周2 尹金亮2 潘富停2
(1 中电投河南分公司 河南郑州 450000;
2 平东热电有限公司 河南平顶山 467021;
开封京华发电公司 河南开封475000)
摘要:平东热电有限公司210MW机组为国产首台旋转隔板调节供汽的大型抽凝机组,同型多台机组出现旋转隔板卡涩和旋转隔板拐臂由于过力矩断裂问题,由中电投河南分公司和哈汽厂组成专家组,对旋转隔板故障原因进行了分析,制定了旋转隔板处理方案并在大修中实施,取得显著成效。
关键词:抽汽式汽轮机;喷嘴配汽式旋转隔板;供热工况;Deva合金材料;
1 前言
河南平顶山平东热电有限公司“以大代小”工程项目,由于其供热为工业用汽和城市采暖系统合一其采暖期抽汽量约700T/H,电厂位于市中心,“以大代小”工程项目机组容量限制在200MW级,采用成熟的超高压、一次中间再热、高中压合缸、两缸两排汽轮机组,汽轮机厂开发设计了具有旋转隔板调节级的大流量(最大370 T/H,调压力0.7845-1.275MPa)的抽凝型汽轮机。其两台机组为哈尔滨汽轮机厂设计生产的N210/C140-12.75/535535型超高压、一次中间再热、高中压合缸、两缸两排单抽汽轮机组,本机最大纯凝工况电功率为224410KW,最大工业抽汽370t/h,最高抽汽压力1.275MPa,汽轮机带一段调节抽汽及六段回热抽汽,其抽汽为喷嘴配汽式旋转隔板级单阀控制抽汽流量和压力系统,旋转隔板采用压力卸载方式,同时采用Deva自润滑Fe-Ni合金作为密封面材料,以减少摩擦阻力,从而使旋转隔板的驱动力矩减少,结构紧凑,其旋转隔板润滑材料、工作压力和温度属国内200MW级抽凝机组中首次使用,填补了国内200MW等级抽汽机组的空白,新的抽汽调节方式对于抽汽机组的经济性和可靠性有很大的影响,它的运行和技术改造情况可以为国内后来建设的同类型机组的制造提供有益的经验。
2 平东公司210MW旋转隔板抽汽系统主要设计特点
国产大型抽凝125MW-600MW单抽或双抽机组,均为两缸两排汽,在实现抽汽的调节方式上 381
有很大的不同。一是135MW-600MW级大容量抽汽供热机组一般采用在汽轮机通流部分中设置调节阀调节级来实现抽汽的调节,采用调节阀门调节级可克服一些50MW及以下机组用旋转隔板调节抽汽时在个别电厂“卡死”,同时亦提高了该调节级的经济性;其次是135MW~600MW级大容量抽汽供热机组除了在通流部分中设置调节阀门调节级来进行调节抽汽外,还在相应的抽汽管道上设置调节阀门,配合汽轮机通流部分中的调节阀门调节级进行调节抽汽。
国内的50MW及以下的抽汽系列机组大多采用在机组通流部分中设置旋转隔板调节级来实现抽汽的调节,调节旋转隔板是抽汽供热式汽轮机特有的结构,旋转隔板的优点是汽缸结构简单,转子长度缩短;缺点是结构复杂,旋转隔板通流部分的结构要比抽汽调节阀复杂得多,间隙安装时,易超差,在压差大的时候,容易卡涩,降低了机组的安全可靠性。
2.1 旋转隔板和连杆机构
调节旋转隔板分为喷嘴配汽式和节流配汽式两种,本机采用旋转隔板来控制抽汽的流量和压力。调节旋转隔板是由转动隔板、罩环和静止隔板组成,转动隔上有大小及间距不同的叶栅,通过双侧进油油动机双侧进油油动机带动连杆机构来实现对转动隔板的操纵使旋转隔板快速开启和关闭,确保机组的安全可靠性,转动隔板位置不同,隔板上的喷嘴开启的通流面积不同,以控制进入低压部分的蒸汽流量,最小排汽工况,通过80t/h的流量,以冷却低压部分,避免过热。
2.2 旋转隔板的压力卸载方式
旋转隔板的压力卸载原理为:其罩环“K”平衡室压力,由于罩环间隙“E”设计为0.38-0.43mm,其通流面积远小于于级后相连通的罩环平衡室平衡通道“Q”,所以罩环“K”平衡室压力为级后压力;同时采用自润滑的材料(P)作为静止隔板的密封材料,转动隔板与静止隔板形成密封腔室,由平衡通道“Q” 于级前相连通见图一。
其平衡动态过程为:由于级前压力高于级后,转动隔板存在向后的压力,并且间隙“E”变大,罩环“K”平衡室增大,由于罩环“K”平衡室的压力卸载作用,变成转动隔板后压力大与前面,当转动隔板与静止隔板密封良好时,表现为转动隔板向前的运动使转动隔板与静止隔板之间压力下降,最终形成动态平衡。
图一:旋转隔板压力卸载装置前后平衡室汽流流动示意图
2.3 抗磨块(Deva合金材料)应用
在旋转导叶动作时,为了防止二者接触表面磨损,故在易损部位设计抗磨块Deva自润滑Fe-Ni合金,以保护二者接触表面,以减少摩擦阻力(Deva自润滑Fe-Ni合金设计的摩擦系数0.327),从而使旋转隔板的驱动力矩减少,转动隔板与静止隔板之间抗磨块主要承受转动部分的压力。
382【旋转隔板对中压缸效率影响】
图二:旋转隔板结构简图(所示尺寸均为制造厂设计图纸尺寸)及
3 故障现象及原因分析
3.1 调试期曾出现旋转隔板卡涩现象
平东公司#6、7供热汽轮机旋转隔板在供热调试期间曾出现卡涩在54%位置不能调压现象;本型汽轮机在停机后盘车状态旋转隔板处动静碰磨现象。表现为致使三段抽汽不能参于调节,造成抽汽时旋转隔板不能关小,抽汽压力低,不能保证供汽需要;不抽汽时,旋转隔板不能开大,又无法多带电负荷,严重威胁机组的安全经济运行。
在汽轮机盘车状态,开关旋转隔板油动机后产生盘车电流增大和摆动,严重时盘车盘不动转子。
3.2 旋转隔板卡涩造成杠杆轴断裂问题设备检查情况
2007年8月25日对平东公司两台机组机组进行供热调试,发现低压油动机关闭到位,旋转隔板汽缸外杠杆动作,但供热压力、电负荷不变。停机后检查。发现杠杆轴在花键结构起始处断裂,断裂位置离花键右端部(即油动机杠杆端)约10mm,断裂基本发生在一个圆截面上,此处花键公径ф90mm。见照片。旋转隔板的转动环、罩环及静环(隔板体)存在不同程度的严重变形,旋转隔板各部设计间隙见图二。
首先,罩环与转动环之间轴向间隙,设计值为0.38~0.43mm,转动环外圆与罩环轴向间隙测量值为,上半部分均小于0.05mm,下半部分左下方一处小于0.05mm,其余在0.40mm左右;罩环内圆与转动环轴向间隙测量值为,上半部分左侧中分面附近为0.50mm,其余部分均不大于0.30mm,弧顶部位仅为0.05~0.10mm。
其次,转动环内弧与静环(隔板体)配合槽道轴向间隙,设计1.00mm,实测整圆均为0.05mm不过,间隙严重偏小。
第三,转动环外弧与静环(隔板体)Deva自润滑Fe-Ni合金密封面存在间隙,不能形成密封。
3.3 原因分析
平东#6、7机组与华北某热电厂机组为同型号机组,均为哈汽厂生产制造,出厂序号为:平东#6、7机组为#1、2机,某热电厂#10、11机组为#4、5机,其在投产后两个月的时间,均由旋转隔板故障而停机后揭高中缸。
383
根据检查结果发现,DEVA合金结合面与动环配合部分,安装间隙远大于设计值(D值设计为
1.40-1.60mm,本次现场实测为3.20—3.4mm mm)其间隙有较大改变,由于远大于设计间隙值,使旋转隔板静环DEVA合金密封面与动环配合部分不能有效形成有效密封,不能使旋转隔板的轴向压力卸载,在进行抽汽调节时,动环前后压差增大,同时,动环与罩环轴向间隙E值设计为0.38~0.43mm与单缸50MW供热机组设计值相同,汽轮机厂放大设计后,没有考虑50MW等级抽汽温度(270℃)到200MW等级其抽汽参数为再热后第一级温度较高(抽汽温度430℃)的变化,旋转隔板级组膨胀后造成动静消失,故判定为DEVA合金结合面与动环配合部分活动安装间隙大于远大于设计间隙,不能形成有效的密封,一方面不能使转动环轴向压力卸载,另一方面DEVA合金结合面与动环不能有效配合定位和支撑,使动环在H处受力,严重咬死,同时使旋转隔板的转动环、罩环及静环(隔板体)造成变形。而解体后发现罩环E值处磨损不太严重,只存在局部拉毛问题,其为旋转隔板变形(波浪式变形)引起动、静隔板拉毛。
所以DEVA合金密封面与动环配合部分是否能形成有效良好的密封是主要原因,当密封良好轴向压力卸载正常,旋转隔板调节工作正常;当密封不好,轴向压力卸载变差,旋转隔板变形卡涩,其密封是否正常和旋转隔板变形互为因果,当旋转隔板严重变形,密封不能形成,轴向压力不能卸载,将发生动、静隔板咬死和旋转隔板拐臂由于过力矩断裂的事故。当旋转隔板严重径向变形,出现在汽轮机盘车状态,开关旋转隔板油动机后产生盘车电流增大和摆动,严重时出现盘车跳闸现象。
4 改进方案及修复程序
经计算,对旋转隔板静环隔板DEVA合金面进行车削1.60mm,旋转隔板变形进行机械加工、将静环隔板与转动环之间间隙F,H值由1.00mm 和2.00mm分别放大到1.85mm 和2. 05mm,罩环与转动环之间轴向间隙E值,由原设计值为0.38~0.43mm放大为0.70—1.00mm,对旋转隔板传动杠杆进行了更换。
4.1 首先对转动隔板进行瓢偏测量:
在消除瓢偏后,确定加工尺寸,转动隔板内外环径向、圆周变形量测量部位示意图见图三,经过瓢偏测量,转动隔板变形量不大,内、外环均没有出现变形,内环端面圆周架百分表测量,跳动0.21mm,内环相对外环向后(静环方向)轻微变形0.19mm。外环径向没有出现变形,外环端面圆周架百分表测量,跳动0.18mm,没有对转动隔板进行机械加工,只对磨损严重处(拉毛部分)进行手工打磨圆滑过渡处理。
384
图三:转动隔板各部间隙示意图
4.2 动环与隔板体轴向间隙F、H值:
由于现场解体后,两侧间隙都已经咬死拉毛。图纸规定动环与隔板体轴颈小端面轴向间隙F值为(1.00mm),实测为0,改造方案规定可以放大到1.50mm左右;
图纸规定动环与隔板体轴颈大端面轴向间隙为H值为(2.00mm),实测为0,改造方案规定可以放大到2.05mm左右;
在对其车削后将尺寸加大到:F=1.85mm,H=2.05mm。现在间隙分别为1.85mm 和2.05mm。
4.3 罩环轴向间隙E、X值情况:
设计动环与罩环轴向间隙E、X均为0.38-0.43mm,解体后发现罩环E值处磨损不太严重,只存在局部拉毛问题,实测为0;方案规定可以放大到0.70—1.00mm,组装测量为E值0.85mm。现在上部间隙为1.10—1.20mm,下部间隙为1.20mm。
X值处圆周都有拉毛问题,且无间隙, 方案规定可以放大到0.70—1.00mm,设计同意最大允许不超过1.20mm;组装测量为X值0.90-1.00mm,继续加工车削到最大间隙为1.2mm。鉴于此处加工后无法进行装配间隙测量,采用压铅丝的方法进行,确保X值为1.20mm。
4.4 动环与隔板体径向间隙N:
由于制造厂提供的是静环此处加工公差和转动隔板此处加工公差,静环加工公差为上偏差为-0.20mm,下偏差为-0.35mm,转动隔板上偏差为+0.00mm,下偏差为+0.20mm。这样配合间隙在0.20-0.55mm。现场解体后发现此间隙实测为0,存在局部拉毛问题。在对其手工打磨圆滑过渡后,用塞尺测量中分面两侧间隙为0.50-0.60mm。图纸规定动环与隔板体径向间隙为0.20—0.55mm,经过设计同意,允许放大到单面0.60—0.70mm,继续加工到间隙为0.60-0.70mm(半径间隙)。加工完成后,要把转动隔板在静止隔板上进行组装,对径向配合间隙(N值)进行实际测量,方法为:用百分表推出上、下,左、右总配合间隙,确保直径总间隙为1.20-1.40mm。
4.5 DEVA合金结合面人工研磨处理:
安装间隙大于设计值(D值设计为1.40-1.60mm,本次现场实测为3.20—3.4mm mm),对DEVA进行机械车削,(见附图四)车削总量为1.60mm。然后对DEVA合金结合面进行人工研磨处理,
385
旋转隔板对中压缸效率影响(三)
技师试卷
汽轮机运行与检修专业行业汽轮机运行值班员技师试卷
一、判断题(正确的请在括号内打“√”,错误的请在括号内打“³” 每题2分,
http://m.zhuodaoren.com/shenghuo321562/
推荐访问:汽轮机旋转隔板 旋转隔板原理